Le Lean Six Sigma
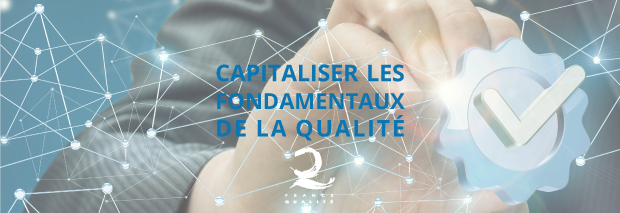
Le Lean management et le 6 Sigma sont 2 systèmes de management qui demandent de changer les schémas de pensée, d’abandonner la hiérarchie classique et d’instaurer la transparence partout. Le Lean vise à augmenter la valeur ajoutée et éliminer les gaspillages. Le 6 Sigma se concentre sur la réduction des erreurs. La combinaison des 2 méthodes donne des résultats extraordinaires.
Le Lean Management
Lean signifie en anglais « maigre », « sans gras », « minceur ». Cette démarche de management tient son nom de chercheurs du MIT qui ont étudié le système de Toyota, le TPS – Toyota Production System, qui remonte aux années 1950. Elle repose sur 5 principes fondamentaux :
- L’analyse de la valeur ajoutée : la valeur ajoutée est définie par le client final (produit, besoins, prix, moment, lieu).
- La chaîne de valeur : la chaîne de valeur concerne l’ensemble des actions nécessaires pour délivrer le produit/service. L’analyse de la chaîne de valeur du produit/service permet de mettre en évidence des gaspillages.
- L’obtention d’un flux : nous pensons le plus souvent en vision verticale (fonctions, services) et en silos, ce qui tend à regrouper les tâches similaires par liste. Il faut plutôt raisonner en mode transversal via des processus inscrits dans une vision globale. Nous devons organiser des flux transverses d’activités pour générer de la valeur.
- Le passage du « pousser » au « tirer » : la production est organisée en fonction des prévisions de vente, par lots, selon les capacités locales de production (« pousser »). À l’inverse, le principe « tirer » signifie que personne en amont ne produit tant que le client en aval ne l’a pas demandé. Le Lean impose donc de passer d’un système de production basé sur les prévisions de vente à un système organisé selon les demandes réelles des clients.
- La perfection : les quatre premiers principes impliquent des changements profonds dans l’entreprise et l’organisation du travail. Mais pour assurer une transformation durable, il est essentiel de mettre en place un système de management adéquat.
Le 6 Sigma
Début 1979, Paul Gavin, le CEO et fondateur de Motorola fixe un objectif : « réduire les défauts par 10 en 3 ans ». Au début, la démarche 6 Sigma était centrée sur la résolution de problèmes puis est venue la notion de mesure : 6 Sigma, c’est 3,4 défauts par million. Pleinement déployée vers 1986, Motorola a investi 25 M$ (formations, accompagnement) avec un retour sur investissement multiplié par 10 en 12 mois.
La démarche 6 Sigma est un système de management focalisé sur l’amélioration de la performance avec :
- Une organisation en mode projet,
- Une focalisation sur les clients,
- L’amélioration des processus,
- La mesure systématique avec des faits et les données.
La démarche s’appuie sur des acteurs certifiés : les Green Belt et les Black Belt (4 semaines de formation). Un système de reconnaissance des personnes (Green et Black Belt) et des équipes impliquées est mis en place au niveau individuel et collectif.
Le Lean 6 Sigma
Engager une démarche Lean 6 Sigma, c’est combiner les 2 méthodes et donc à la fois éliminer les gaspillages et réduire le nombre et la variation des erreurs. Il s’agit de s’appuyer sur les 5 principes du Lean management et de dérouler la méthode DMAIC (Define, Measure, Analyse, Improve, Control). Cette trame permet d’améliorer les processus d’une manière systématique.
En résumé, le Lean 6 Sigma c’est : comment bien faire du premier coup, sans délai inutile, sans dépenses superflues et bien entendu pour la plus grande satisfaction des clients.
Les gaspillages
L’entreprise produit des gaspillages colossaux tout au long de son processus de production. Le Lean 6 Sigma permet de réduire d’une manière considérable ces gaspillages dans les 8 domaines suivants :
- Attente : d’un matériel ou d’une décision
- Transport : le déplacement d’un matériel qui ne génère pas de valeur ajoutée
- Processus : la manière de procéder ne produit pas la qualité du premier coup
- Stock : le stock génère de la perte d’espaces, des frais généraux, des encours de production et des immobilisations financières pour de la matière inutilisée
- Mouvement : tout geste d’un opérateur qui ne contribue pas directement à l’ajout de valeur dans le produit fini
- Non-qualité : ce sont des pièces défectueuses induisant des actions chronophages de reprise
- Surproduction : c’est la conséquence d’une production faite en avance, plus vite ou en plus grande quantité que la demande du client
- Talents : c’est ne pas utiliser pleinement l’intelligence des opérationnels qui travaillent sur le processus.